
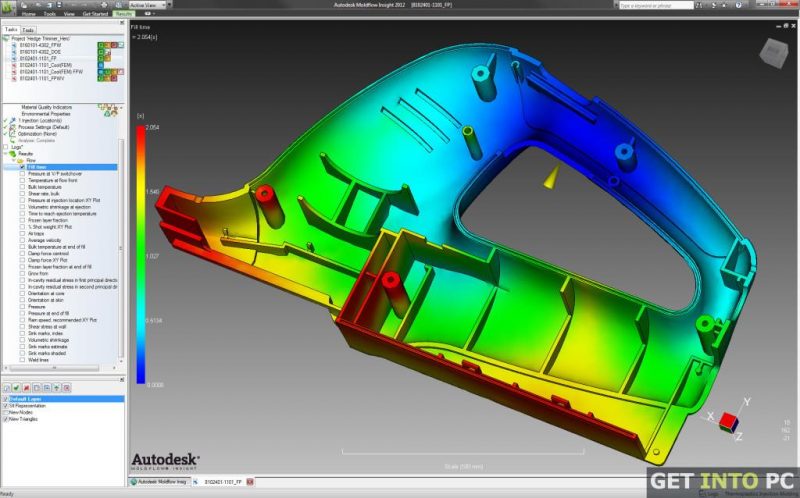
Moldflow does not need to be installed on the same computer as Simulation Mechanical.The only time that the model needs to be exported to Moldflow is if the position or shape of the plastic parts change. In theory, the mesh can be changed in Simulation Mechanical without needing to export the revised model to Moldflow. Once the Moldflow results are computed, the Simulation Mechanical model can be analyzed multiple times to test different boundary conditions, loads, and so on.This may affect how fine you make the mesh density to satisfy the needs of the injection model. Therefore, all curved surfaces are approximated as faceted faces - the finer the mesh, the more accurate the approximation of the curved surface. Moldflow generates its own mesh based on the outside surface mesh from the part in Autodesk Simulation Mechanical.Note that results related to the Moldflow analysis, including the orientation of the fibers, must be viewed in Moldflow. If the material was changed in Moldflow, the new material will show in Simulation Mechanical after the stress analysis is performed. Start the analysis ( Analysis Analysis Run Simulation).Select the appropriate file and click Open.Click the cell showing the Associated Moldflow Study File for the part.If any Moldflow results are in a study different than the one to which the Autodesk Simulation model was exported, browse for the location:.

Refer to the Moldflow help documentation for instructions. Then, perform a Fill+Pack analysis on each study (each part from Simulation Mechanical). Open the project and make any changes as desired to the setup.If Moldflow was not started when the model was exported from Simulation Mechanical, start Moldflow.Spaces, dashes, and other special characters in the names are changed to underscores (_) in the Moldflow name. The default name for each study is the Autodesk Simulation part number and part name. The folder and project names default to name of the Autodesk Simulation model. The Moldflow project is located in a folder underneath the user-selected folder. Adviser also supports CTE, but does not support residual stress. Autodesk Moldflow Adviser performs a subset of the analyses available with Moldflow Insight.Autodesk Moldflow Insight performs various analyses, including both residual stress and coefficient of thermal expansion (CTE).You must use one of the following supported element types for the Simulation Mechanical plastic parts (that is, the parts to which the Moldflow material model and Moldflow results are applicable):.Although this technique is commonly used for stress analysis, the injection molding process is rarely symmetrical in nature. Though Simulation Mechanical and many CAD applications allow a part to consist of multiple volumes, this practice must be avoided to ensure interoperability with Moldflow. Multiple parts (assemblies) are allowed as long as each individual part consists of a single volume. Each part within a Moldflow model must consist of a single contiguous volume.The following restrictions apply regardless of which workflow you choose: There are two workflows outlined herein, depending upon whether or not the Moldflow analysis has already been setup and run at the time the Simulation Mechanical model is started.
#Autodesk cad manager tools simulation moldflow how to
How to Use Moldflow Results in Simulation Mechanical
